10 outstanding methodologies for reengineering of business processes
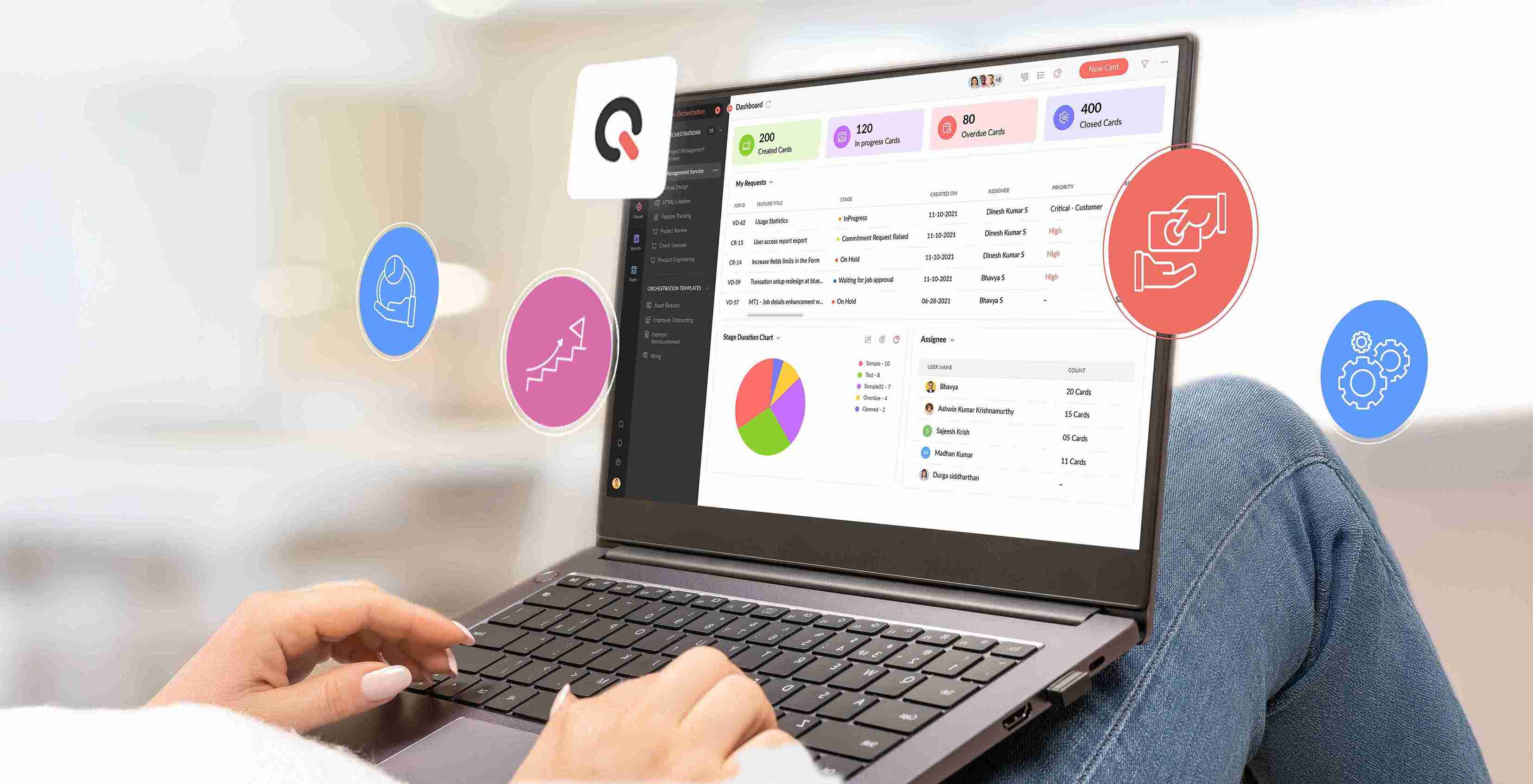
Companies are always trying to find new ways to better their processes. Process improvement methods optimize operations to work towards achieving set goals, eliminating waste, and increasing efficiency within a business organization.
This post discusses 10 effective methodologies that can change the face of your business.
1. Lean
Lean is a method of working where maximum value is obtained from the resources used, and waste is minimal. While it originated in manufacturing, the core features of Lean have also been implemented in other industries.
Lean seeks to provide innovative products and services through the entrenchment of high-value tasks and listening to customers by removing unimportant aspects.
Some of the important concepts of Lean
- Value definition: One of the most important concepts in Lean is satisfying the customers, which means delivering value to them. This means determining what enhancements or services do or do not matter to your customers and concentrating on making your customers happy.
- Elimination of waste: Waste in Lean can happen in many forms and is commonly called "Muda." The waste Lean identifies and examines are uncontrolled output levels, delays, unnecessary movement, excessive order preparation and processing, stockpiling, people's activities, and errors. By carefully analyzing and removing all waste, the organization's processes can be more efficient.
- Continuous improvement: One of the philosophies adopted in Lean is known as the practice of Kaizen, which refers to continuous improvement. Here, all employees have opportunities to improve processes, which generates a feeling of ownership.
Lean implementation
Leaders and management have to agree and be prepared for changes when adopting the Lean management approach. It usually starts with educating employees on the basics of Lean, including some tools such as value stream mapping and5S (Sort, Set in order, Shine, Standardize, Sustain). With the help of these tools, teams are able to see and understand processes, eliminate waste, and create action steps for improvement.
2. Six Sigma
This is a quality control method that aims to improve processes and reduce output variability. Six Sigma is a systematic and quantifiable strategy, aimed at achieving a target of only 3.4 defects in a million opportunities through high quality levels.
The DMAIC framework
The DMAIC structure is essential in Six Sigma improvement projects and includes other principles and methodologies.
- Define: Explicitly explain the problem or project, the objectives, and the perceptions of the customers.
- Measure: Obtain information that will identify the current performance level and defects.
- Analyze: Interpret the collected information to establish the main goal of eliminating defects.
- Improve: Come up with and implement relevant responses to the identified scope.
- Control: Set up limits to maintain the improvements and follow up on progress over a given period.
Instruments employed in Six Sigma
Six Sigma is associated with modern statistical techniques, including process mapping, cause-and-effect diagrams, and control charts. These tools help teams understand the nature of their processes and make quantitative fundamental decisions.
Training, certification, and implementation
Most organizations have budgets set aside for training employees on Six Sigma practices, giving rise to the “Green Belts,” “Black Belts,” and “Master Black Belts.” These are the individuals in an organization who will lead projects towards improvement and also train other members.
3. Kaizen
As mentioned earlier, Kaizen is a Japanese word referring to continuous improvement, which, for a business, would refer to ongoing efforts to enhance products, services, or processes.
Principles of Kaizen
- Process first: In the case of a problem, teams using Kaizen do not look for a person to blame; instead, they focus on the processes and how to improve them. This process-oriented approach leads to improvement without resistance.
- Employee involvement: Ideas on improving the organization are not left to top management only. Gather feedback from the bottom to the top by soliciting the opinions of all employees. This participation not only provides important ideas but also encourages and creates a sense of responsibility throughout the organization.
- Standardization: Standardization applies to the organization as a whole. Once changes have been made, that change needs to be applied consistently throughout the company. This provides a platform for future improvements.
Kaizen implementation
The implementation of Kaizen generally includes regular working group meetings called "Kaizen events." Employees can discuss problems and generate ideas. Some organizations form systems that allow employees at every level to suggest ideas.
4. Agile
Agile is a software development practice, although it has branched out into various industries more as a project management area. A central feature of Agile methodologies is building adaptability, teamwork, and customer relations to suit the prevailing circumstances.
Key principles of Agile
- Iterative development: Agile encourages increments, which usually take a brief period and are called sprints. Each breakdown has a limited number of features to allow for faster work and iterations.
- Customer collaboration: Agile thoughts require clients to be in touch constantly in order to learn their wishes and adapt team members' priorities accordingly.
- Adaptability: Agile’s underlying principle is that if you develop plans together, you will be ready to change those plans when new information emerges.
Agile frameworks
Agile methodologies include several frameworks like Scrum, Kanban, and Extreme Programming (XP). Each framework may have its own tools and practices, but all of them are core to the ideologies of Agile.
Agile implementation
In terms of Agile implementation, organizations, in most cases, carry out training and ask the relevant people to form cross-functional teams. Transparency and alignment are preserved through daily pledges and reviews.
5. Total quality management (TQM)
TQM is an integrated approach to long-term success by satisfying customers through quality improvement in every sphere of the organization. This requires the involvement of every individual in the organization for the sake of growth.
Key principles of TQM
Customer orientation: In TQM, quality and customer satisfaction needs to be applied across all activities.
Employee engagement: The quality management strategy is slightly similar to Kaizen. In it, everybody is active in the products' or services' quality improvement efforts.
Focus on processes: In TQM, the improvement process concentrates on enhancing operations and systems to deliver a product or service instead of blaming individuals for defects. This results in more sustained improvements and better quality.
TQM implementation
TQM is a management approach that cannot be successfully adopted without the support of top management and a redirection of the organization’s norms and values. There are several activities aimed at training employees and creating interest in quality improvement, such as training programs and quality circles.
6. Business process redesigning (BPR)
BPR (business process redesigning) refers to the fundamental improvement of the effectiveness and efficiency of an organization by rethinking and redesigning business processes.
Unlike the general strategy of gradual enhancements of features of certain processes, the aim of BPR is the magnitude of the changes on an organizational level rather than the increment of smaller performance improvement measures like costs, quality, service, and speed.
Key elements of BPR
Radical rethinking: In BPR, it is important to completely rethink how a certain outcome can be achieved. This means eliminating unnecessary parts, adding new processes, or even performing operations without human assistance.
Orientation toward processes: BPR is also process-oriented; it focuses on what workflows are carried out and how, rather than the individual tasks.
Use of technology: It is evident that information technology has a significant impact on BPR. Organizations prefer to use technology that will best implement the altered processes for optimum results.
BPR realization
BPR realization starts with a careful examination of how things are done with an objective to look for places to make drastic changes. Most of these changes require people from all spheres of the organization to work in teams. Once those places are identified, all teams should work towardimplementing those changes, however they may look.
7. Theory of Constraints (TOC)
The Theory of Constraints, as its name suggests, aims to pin down and better the single most significant limiting factor within a process. Focusing on this constraint helps improve performance in any organization.
Key steps in TOC
Identify the constraint: The aim here is to identify the element causing the most waste in the process.
Exploit the constraint: Perform the activities that create the constraint at full capacity.
Subordinate everything else: Direct other procedures and units to complement the constraint.
Elevate the constraint: There might be more than one step needed to fix the issue; if so, initiate actions to continue to fix the issue causing the constraint.
Repeat the process: When the constraint is removed—and is the number one priority—go back to the first stage to look for the second constraint.
TOC implementation
TOC is very useful in manufacturing and project management. Organizations also incorporate other methods, such as drum-buffer-rope scheduling to control the flow of production.
The Theory of Constraints (TOC) is implemented by identifying the most significant bottleneck in a process and focusing efforts on improving that constraint. By streamlining the flow around this bottleneck, organizations can enhance overall efficiency. Drum-buffer-rope (DBR) scheduling supports TOC by regulating production pace (drum), protecting the system with buffers, and synchronizing activities (rope). This method ensures smooth production flow, minimizes delays, and maximizes throughput, boosting operational performance.
8. Value stream mapping (VSM)
VSM is a means of conducting analysis and design on the ordering, direction, and flow of materials and information in a process. VSM introduces organizations’ activities by recognizing waste, inefficiencies, or improvement opportunities.
Implementing value stream mapping
Specify the product or process: VSM should be concerned with procuring the product or the processes that will provide a product to the customer. What is within the scope of VSM is, therefore, dependent on what the paperwork says is the product.
Removing and reorganizing functions: This is the process by which VSM case studies are usually done. The current situation in VSM enables all current state maps to be made in every case.
Flow maps: The next task here is to do a couple of flow maps. In Value Stream Mapping, processing people, machines, parts, and information—every desired asset gets its place, and every process is tied to it.
Future state maps: VSM, when performed in isolation, represents the system in perfect form, even if such a picture is sometimes unrealistic. Therefore, eight-day plans are still being considered per product development in VSM. Making future state maps describes the situation proposed after all the changes have been made.
Value Stream Mapping and process reengineering methods are employed to streamline some business processes. Based on reported or recalled observations of the work environments, DFSOM consists of efficient structures aimed at reconstructing VSM methodology.
When it appears as a technique, a scenario for VSM is integrated into a combined methodology that quantifies costs and preserves sequences. Reimpressions on VSM serve as an additional control of the recent 5S on VSM. Implementation of VSM
VSM workshops are conducted using teams of people from different functions in the organization so as to list more attributes. Organizations can create good maps that reflect their processes by involving various stakeholders.
Implimentation
To implement Value Stream Mapping (VSM), cross-functional teams participate in workshops to map current processes, identify inefficiencies, and highlight improvement opportunities. By involving key stakeholders from different departments, organizations can create detailed and accurate maps that reflect real workflows.
This collaboration ensures a comprehensive view of processes, enabling better decision-making, streamlined operations, and a clearer path toward optimizing productivity and eliminating waste across the value stream.
9. Total productive maintenance (TPM)
Total productive maintenance (TPM) is the concept that all employees should be involved in the productive maintenance of an asset for its optimal utilization. The entire organizational population, from a machine operator to management, takes part in maintenance.
Key principles of TPM
- Employee empowerment: The private operators within the normal business limit will be responsible for managing their non-costing maintenance, moreover generating in-house incentives for such activities.
- Preventive maintenance: TPM takes care of problems in advance with respect to maintenance and ensures that breakdowns are minimized.
- Continuous improvement: Like other methodologies, TPM helps achieve incremental changes in work and equipment reliability.
TPM implementation
In most cases, implementing TPM will involve teaching employees maintenance practices and developing maintenance calendars. Other institutions may form units responsible for assessing and enhancing asset performance.
10. Benchmarking
Benchmarking’s objective is to develop a procedure for internal business measures that correspond to external measures, which can be rated as industry best practice standards. Once performance gaps are identified, setting performance objectives and working towards them becomes easier.
Steps in benchmarking
- Identify key metrics: Ask which organization or industry performance metrics are most critical.
- Select benchmarking partners: Seek out companies that shine in the metrics you identified.
- Collect data: Gather your organization’s performance metrics, the performance metrics of the selected benchmarking partners, or both.
- Analyze performance gaps: Identify any performance discrepancies through performance studies and assess the areas that are lacking.
- Implement improvements: Strategies to address each performance gap identified will be elaborated on and executed.
Benchmarking implementation
Benchmarking is a relative process that can be carried out periodically to block losses for organizations. It embraces a spirit of change and the desire to learn more.
To implement benchmarking, organizations periodically compare their processes, performance metrics, and practices against industry leaders or best-in-class standards. This relative process identifies gaps, promotes a culture of continuous improvement, and helps block inefficiencies.
Through change and constant renewal of knowledge on the process, companies can use benchmarking to enhance performance, drive innovation, and stay competitive in an evolving market.
Conclusion
Business organizations that want to improve their operations and ensure efficiency can do so by applying process improvement strategies. The adoption of one or more of these methodologies helps create an environment for continuous improvement while freeing up employees and, in the end, providing more value for clients. Whether you wish to implement Lean, Six Sigma, Agile, or some other methodology, the important thing is to continue measuring and improving your processes.
By learning and utilizing these tools, introducing changes in your organization will no longer be an impossible and frustrating endeavor. Don’t forget that process improvement is a journey; there are no one-off actions that can ensure a boost in performance and productivity—only constant processes.
Enjoying your reading?
Enjoy organization and visibility too!
Qntrl can help you organise, control and improve production and projects in your team.